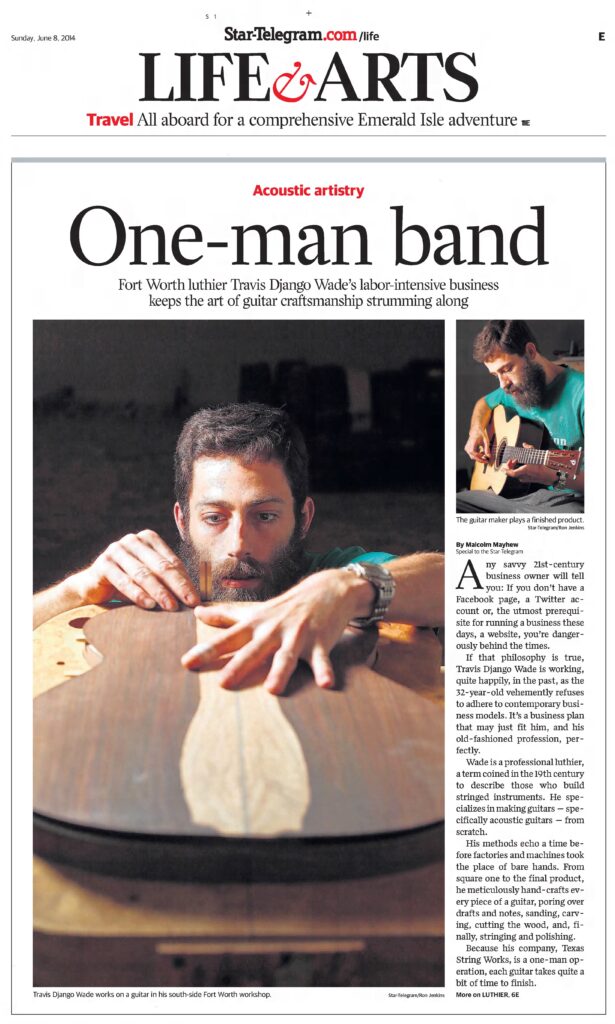
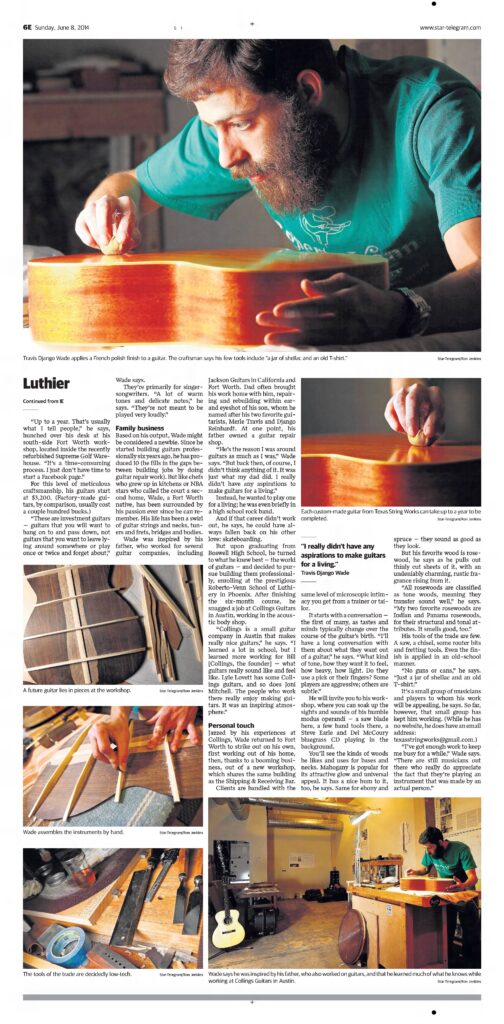
Any savvy, 21st-century business owner will tell you: If you don’t have a Facebook page, a Twitter account or, the utmost prerequisite for running a business these days — a website — you’re dangerously behind the times.
If that philosophy is true, Travis Django Wade is working, quite happily, in the past, as the 32-year-old vehemently refuses to adhere to contemporary business models. It’s a business plan that may just fit him, and his old-fashioned profession, perfectly.
Wade is a professional luthier, a term coined in the 19th century to describe those who build stringed instruments. He specializes in making guitars — specifically acoustic guitars — from scratch.
His methods echo a time before factories and machines took the place of bare hands. From square one to the final product, he meticulously hand-crafts every piece of a guitar, poring over drafts and notes, sanding, carving, cutting the wood and, finally, stringing and polishing.
Because his company, Texas String Works, is a one-man operation, each guitar takes quite a bit of time to finish.
“Up to a year. That’s usually what I tell people,” he says, hunched over his desk at his south-side workshop, located inside the recently refurbished Supreme Golf Warehouse. “It’s a time-consuming process. I just don’t have time to start a Facebook page.”
For this level of meticulous craftsmanship, his guitars start at $3,200. (Factory-made guitars, by comparison, usually cost a couple hundred bucks.)
“These are investment guitars — guitars that you will want to hang on to and pass down, not guitars that you want to leave lying around somewhere or play once or twice and forget about,” Wade says.
They’re primarily for singer-songwriters. “A lot of warm tones and delicate notes,” he says. “They’re not meant to be played very loudly.”
Based on his output, Wade might be considered a newbie. Since he started building guitars professionally six years ago, he has produced 10 (he fills in the gaps between building jobs by doing guitar repair work). But like chefs who grew up in kitchens or NBA stars who called the court a second home, Wade, a Fort Worth native, has been surrounded by his passion ever since he can remember. His life has been a swirl of guitar strings and necks, tuners and frets, bridges and bodies.
Wade was inspired by his father, who worked for several guitar companies, including Jackson Guitars in California and Fort Worth. Dad often brought his work home with him, repairing and rebuilding within ear- and eyeshot of his son, whom he named after his two favorite guitarists, Merle Travis and Django Reinhardt. At one point, his father owned a guitar repair shop.
“He’s the reason I was around guitars as much as I was,” Wade says. “But back then, of course, I didn’t think anything of it. It was just what my dad did. I really didn’t have any aspirations to make guitars for a living.”
Instead, he wanted to play one for a living; he even briefly played in a high school rock band.
And if that career didn’t work out, he says, he could have always fallen back on his other love: skateboarding.
But upon graduating from Boswell High School, he turned to what he knew best — the world of guitars — and decided to pursue building them professionally, enrolling at the prestigious Roberto-Venn School of Luthiery in Phoenix. After finishing the six-month course, he snagged a job at Bill Collings Guitars in Austin, working in the acoustic body shop.
“Collings is a small guitar company in Austin that makes really nice guitars,” he says. “I learned a lot in school, but I learned more working for Bill — what guitars really sound like and feel like. Lyle Lovett has some Collings guitars, and so does Joni Mitchell. The people who work there really enjoy making guitars. It was an inspiring atmosphere.”
Jazzed by his experiences at Collings, Wade returned to Fort Worth to strike out on his own, first working out of his home, then, thanks to a booming business, out of a new workshop, which shares the same building as the Shipping & Receiving bar.
Clients are handled with the same level of microscopic intimacy you get from a trainer or tailor.
It starts with a conversation — the first of many, as tastes and minds typically change over the course of the guitar’s birth. “I’ll have a long conversation with them about what they want out of a guitar,” he says. “What kind of tone, how they want it to feel, how heavy, how light. Do they use a pick or their fingers? Some players are aggressive, others are subtle.”
He will invite you to his workshop, where you can soak up the sights and sounds of his humble modus operandi — a saw blade here, a few hand tools there, a Steve Earle and Del McCoury bluegrass CD playing in the background.
You’ll see the different kinds of woods he likes and uses for bases and necks. Mahogany is popular for its attractive glow and universal appeal. It has a nice hum to it, too, he says. Same for ebony and spruce — they sound as good as they look.
But his favorite wood is rosewood, he says as he pulls out thinly cut sheets of it, with an undeniably charming, rustic fragrance rising from it.
“All rosewoods are classified as tone woods, meaning they transfer sound well,” he says. “My two favorite rosewoods are Indian and Panama rosewoods, for their structural and tonal attributes. “It smells good, too.”
His tools of the trade are few. A saw, a chisel, some router bits and fretting tools. Even the finish is applied in an old-school manner.
“No guns or cans,” he says. “Just a jar of shellac and an old T-shirt.”
It’s a small group of musicians and players to whom his work will be appealing, he says. So far, however, that small group has kept him working. (While he has no website, he does have an email address: texasstringworks@gmail.com.)
“I’ve got enough work to keep me busy for a while,” Wade says. “There are still musicians out there who really do appreciate the fact that they’re playing an instrument that was made by an actual person.”
Originally published May 7, 2014. Note: After this story was published, Travis started a website, wadeguitar.com.